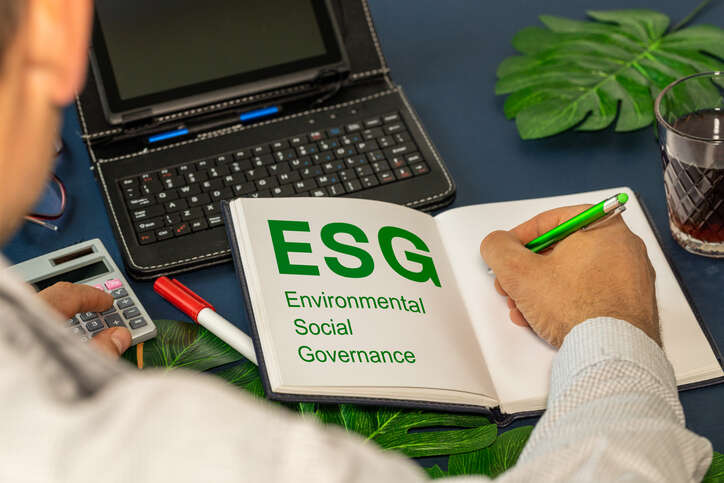
How Longer Product Lifecycles Are Boosting ESG Initiatives
One of the most consistent questions organisations face when considering environmental and social governance (ESG) is ‘what does it really mean to me?” While this is perhaps not the best way to look at ESG, going against the very idea of what ESG means, there are good reasons to take it very seriously.
For one, as a Bain & Company report in April revealed, “strong ESG performance is a sign of a strong business.” The report cites that these companies tend to improve carbon emissions, use renewable energy, and have more diverse leadership and talent. “Working together like the gears of a pocket watch, these activities correlate with improvement in financial and operational results, including higher profitability and revenue growth, customer satisfaction, and employee satisfaction,” says the report.
The challenge, however, facing many businesses is how to get there? Certainly, the E in ESG can be difficult to measure and manage consistently, while a reliance on energy suppliers can be challenging in staying on top of costs and renewables consumption. There is an argument that organisations should focus on the factors that they can directly control and understand – and that makes a lot of sense.
For any organisations selling and servicing products, so much cost and carbon emissions are tied-up in production and post-sales services. This is where businesses can have a big impact on ESG initiatives through a greater understanding of product lifecycles and maintenance needs.
Right here right now
Field service management (FSM) tools enable companies to be more sustainable and reduce emissions via improved first-time fix rates and remote triage and troubleshooting. This reduces truck rolls, which means less fuel consumption, more efficient dispatching, and visibility into the supply chain.
This also allows for more effective parts management. Having the right parts in the right place at the right time, sounds like a common-sense thing to do but in reality, it can be difficult and costly if not managed properly. Understanding customer machine performance in real-time, using AI-driven predictive maintenance, for example, can help organisations manage services more efficiently.
One of the most obvious benefits is better planning, which means less costly knee-jerk emergency shipping of parts, a reduction in paper-based processes (which also means less errors) and a more optimised field service team of engineers.
But it is in improving product lifecycle rates where businesses can achieve significant financial and carbon savings. Each product has direct and indirect carbon impacts and there are lifecycle analysis (LCA) tools to measure this – it’s worth pointing out here that the Ellen McArthur Foundation warns against the short-termism of LCA measurements and not using them as the single source of truth. However, as the Foundation also points out, these tools can be valuable if used correctly.
This is important because you can only really manage what you can measure. Understanding how product lifecycle impacts emissions is key to knowing where to focus efforts. Organisations can use FSM to manage the processes (reverse logistics, depot repair and so on) that enable them to refurbish and remanufacture products but knowing which products are the biggest offenders when it comes to emissions, enables prioritisation.
Intelligence by design
Of course, using performance data captured in FSM enables organisations to feed intelligence back to product designers to help improve energy consumption, product durability but also for maintenance. If a product is designed to enable easier swap-out of parts or for disassembly, it will only help in reducing cost and carbon impacts.
A circular approach demands new thinking in product development but it is through FSM that organisations can really understand the real-world impacts of change on customers. How customers use machines can have a bearing on product lifecycles and should be factored into any new development.
We now live in an age of data intelligence and field service is no different. FSM is front and centre in analysing and enabling data in helping organisations make significant changes to how they operate. As Pitney Bowes reveals, FSM enabled the business to reduce inventory by as much as $4.7m after integrating data from its parts management system and FSM systems. Schneider Electric has also seen significant benefits from using FSM. Digitalisation resulted in a 70% reduction paper-based processes.
As businesses either embark on an ESG journey or continue to implement an ESG strategy, understanding product lifecycles should be a big part of the process. The repair, re-use and recycle idea should apply, as much as possible, where possible. Service teams are at the heart of this but whether or not they can help reduce carbon and boost ESG initiatives will come down to the quality of their FSM data.