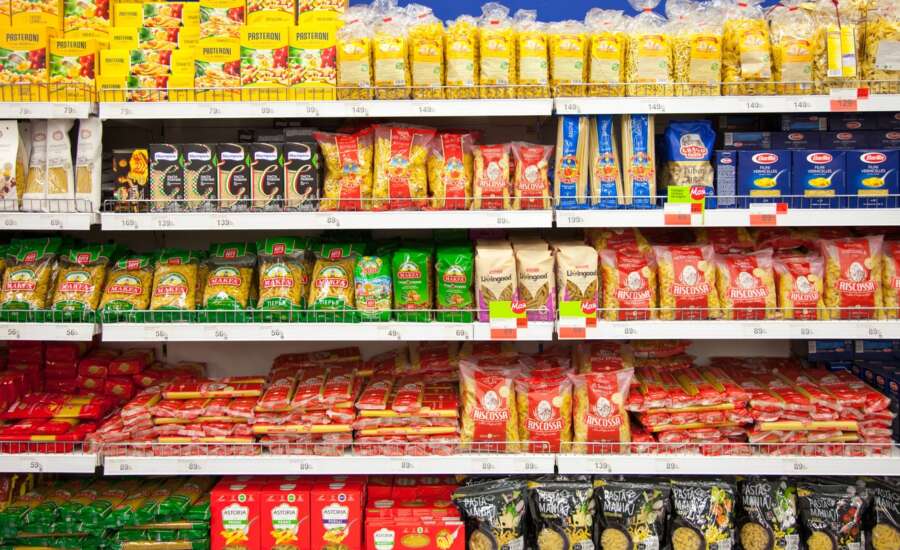
By Emma Lewis, Tax Cloud
“Every year the UK generates more than two million metric tons of plastic packaging waste. This equates to roughly 36 kilograms of plastic packaging waste per person.” – Statista
Google “plastics recycling in 2022” and the first thing you notice is the sheer number of business conferences coming up on this very subject. It’s certainly a hot topic, with companies across the industry clamouring to make the plastic in their products fully recyclable.
There’s no getting away from it. Plastic in food packaging is tough to beat, thanks to its sheer durability and cheapness to produce. The problem is, recycling plastic it isn’t always easy. In fact, just 16% of plastic waste is recycled to make new plastics, while 40% goes to land fill, 25% is incinerated and 19% is dumped.
The good news is this is changing, with recycling facilities becoming steadily more advanced. But the next big challenge for polymer chemistry is to not just recycle but to actually turn plastic back into its basic components, like oil. It’s something called “infinite plastics”.
To infinity and beyond
Plastic has traditionally been recycled in a kind of downward spiral rather than a loop. It’s generally recycled mechanically – sorted, cleaned, shredded and melted – before being remoulded. But each time this happens, the quality of the plastic declines. Once it’s below a certain standard, it’s no longer suitable for food grade use, while its lack of strength and viscosity makes it hard to work with. Essentially, plastic to be used in food packaging can only be recycled a very finite number of times before it’s obsolete.
Chemical recycling (also called “feedstock recycling“) is an emerging industry that looks to tackle this. Technology is being developed that works to break down the plastic into its chemical building blockswhich can then be used for fuel and other purposes.
Feedstock recycling is the best process by which this can happen. It’s a way of recycling plastic by using heat to break down the polymers into simpler molecules.
So how does it work?
Take the humble plastic drinks bottle. You’ve finished with it, so it goes into your recycling bin for collection. It’s then sorted at the nearest facility, either by hand or mechanically, depending on what type of plastic it’s made from.
Once sorted, your bottle is washed and shredded into a bale so it’s easier to transport. So far so good – and pretty conventional. But then the chemical recycling process starts and this is where things get interesting.
The plastic that your bottle used to be made of will now be taken to a pyrolysis centre for melting down. It’s heated to a very high temperature inside a pyrolysis reactor. The heating turns the plastic into a gas which turned into an oil-like liquid when cooled and condensed. Finally, this liquid is distilled into its component parts to be used for a range of different purposes.
Different chemical recycling techniques are being trialled around the world. In the UK, the first commercial-scale unit was built in 2020 in Perth, Scotland. Another company based in Swindon, Recycling Technologies, has also designed a pyrolysis machine which turns hard-to-recycle plastic such as laminated plastics, bags and films, into a liquid hydrocarbon feedstock called Plaxx. This Plaxx can then be made into plastic that’s pretty much virgin quality.
In Spain, Plastic Energy has developed two plants with plans to expand its operation into the Netherlands, France and the UK. Its technology will focus on other plastics that are difficult to recycle, including pet food pouches, confectionary wrappers and breakfast cereal bags. Such plastics will be converted into TACOIL which can then be used in making food-grade plastics. Watch this space…
QR codes to reduce the packaging products need
Yes food packaging must be kept to a minimum. But it also needs to do the job it was designed for. Food must be packaged to stay fresh, especially as 6% of global green house emissions are the result of food waste.But it’s a tricky balance to strike.
As well as safety and freshness issues, food packaging for example must, by law, display a list of ingredients the product contains. Often the sheer number of words this requires, especially if there are further instructions or details, can mean the packaging is larger than it really needs to be.
Step in QR codes. The technology isn’t particularly new, but in 2022 onwards we can expect to see them adapted to contain far more consumer information than will ever fit on standard food packaging. Simply by scanning the code with their phone, consumers will also be able to access information about product source, the brand’s business model and ethics and much more. Less packaging, more information.
Packaging automation
Automation speeds up your packaging line for maximum efficiency with fewer people and fewer costs. Throughout 2022 and beyond, automated packaging machinery is expected to become more sophisticated and cheaper to manufacture. Companies will also find that by automating their packaging line they’ll not only increase production but help to guard against staff absence (yes, the dreaded COVID-19) and supply chain issues.
Just recently, Packaging Digest published a great article on some of the most interesting automated packaging advances. It’s well worth a read.
Moving forward
These are just a few of the innovations we’re expecting to see more of in the coming twelve months. It’s by no meansan exhaustive list, with companies working on more sustainable, effective and cheaper ways to meet packaging demand. In the UK, these companies can also benefit from R&D Tax Credits, worth tens of thousands of pounds towards their innovation costs. This in itself has been a huge incentive, and the number of claims is rising.
The COVID-19 pandemic has set the economy back, but the desire for packaging companies to innovate in 2022 is strong.