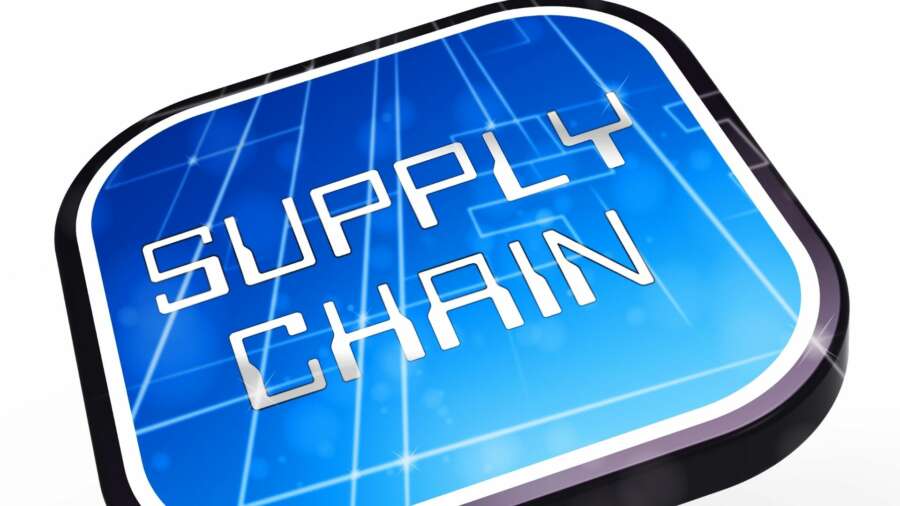
By Rob Sinfield, VP Product, Sage X3 and ISV Success at Sage
Many brands seriously affected by the global pandemic have chosen to change their product and service offerings and transform business models in the name of helping the frontline response. They’ve coped well with the disruption and made a positive contribution, all while keeping the bottom line stable.
However, even as we slowly ease back into business as usual practices, it’s clear supply chain operations have changed for good. While the initial impacts of COVID-19 have been gradually easing, it will take time for the long-term repercussions of the pandemic to emerge. Judging by the last few years of disruptive and unforeseen events, the new normal will be defined by the unexpected.
Going forward, businesses won’t be able to predict everything that will happen. However, they can introduce agile processes and technologies into their supply chain to ensure they have ample time to prepare.
Time for a rethink
A macro-economic change of this magnitude is difficult to predict and it has moved businesses into uncharted territory. Whilst a business might have risk management processes in place to deal with controllable and expected challenges, such as compliance and capacity issues, few have contingency plans for a global pandemic of the like we are experiencing. Even as lockdown measures are eased, local COVID-19 flareups could mean that businesses suddenly need to cope with less staff, falls in productivity, material shortages and changes in consumer spending behaviour.
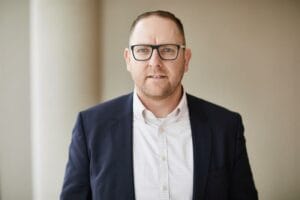
Rob Sinfield
What’s more, COVID-19 has highlighted the connection between supply chains and business success. To illustrate, 200 of the Fortune Global 500 companies have an element of their supply chain in Wuhan. When a lockdown was declared in that one city, it disrupted the supply chains of 40% of the world’s biggest businesses. To stop this happening again, organisations need to know where their vulnerabilities lie and have visibility over them at all times.
Going forward, supply chains need to be more robust and resilient to change. Many businesses – particularly in the manufacturing space – are dealing with significant cost pressures and tight margins. They need the ability to forecast conditions accurately and deal with unexpected changes in demand, before customers and the bottom line feel the impact.
Resilience starts with data
Even as stores begin to reopen, businesses are likely to stay digital-first or even digital-only in the foreseeable future. Retail e-commerce site visits grew to almost 22 billion unique visits at the height of the pandemic, with no lull in sight. The dominance of e-commerce and the growing need to move products around a complex network of warehouses, only strengthens the need for a more transparent and intensively-monitored supply chain model.
To achieve this, it’s crucial organisations utilise the vast amounts of data generated by daily operations and turn it into actionable insight. A sudden drop in demand for certain products could speak to a wider trend, or a fall in output could indicate faults on the production line before they become full-blown malfunctions.
Decisions made on the basis of accurate, real-time data improve plant efficiency, customer service and innovation. Since they can use data more effectively, businesses can make better decisions and have increased agility when managing operations. This allows them to keep delivering even when disruption hits. That’s why 40% of businesses consider data analytics to be one of the most important technologies for supply chain management.
However, a siloed data infrastructure can easily get in the way of a joined-up response to disruption. Supply chains are complex networks comprised of many individual sites. Warning signs and issues are easily missed when this site data isn’t integrated or when local decision-makers fail to share insight.
Businesses should look to enterprise systems which can help them integrate, manage and analyse huge amounts of complex product and operational data. Supported by the right technology, businesses can forecast and report production, consumption and fulfilment. This enables them to reduce spoilage and costs by improving efficiency. Analytics, meanwhile, provides intelligence for when a problem might occur and direction on how to resolve that issue.
An integrated, cloud-based data infrastructure gives frontline staff the ability to connect their day-to-day operations with overall business goals. Increased stock visibility and improved data-sharing ensures items are available whenever and wherever they are needed. With this insight, operational managers can monitor the real-time status of stock levels and locations, adapting product levels as needed to head off disruption.
Don’t respond; take the initiative
Supply chains differ in size and complexity, but all are inextricably linked to the success of their business. With the precedent set by the global pandemic, we may be within reach of a new supply chain model. One where businesses can be agile and responsive to changing policies, regulations and the unexpected.
When collating and analysing data from across the entire supply chain, businesses have an advantage. They can plan purchasing, delivery and maintenance more efficiently, and they have the foresight and agility to resolve supply chain challenges before they occur. Resilience in the new normal means getting ahead of change, not following it.